Digital transformation in manufacturing: Overcoming key challenges with OnScreen Guidance
Overview of digital transformation in manufacturing
Digital transformation is changing the manufacturing industry. New technologies are reshaping how companies operate. Tools such as cloud-based ERP, MES, and PLM systems, along with automation and data-driven insights, are becoming essential. This shift promises more efficiency, better decision-making, and a stronger competitive edge.
However, the journey is not without challenges. Manufacturers must navigate digital skills gaps, software adoption issues, and the need for effective training. In this blog, we’ll explore the importance of digitalization in manufacturing, discuss key components, and examine how companies can overcome common obstacles. We’ll also look at how a digital adoption platform (DAP) like OnScreen Guidance can ease the transition, ensuring a smooth and successful digital transformation.
The importance of digitalization in manufacturing
Digitalization is crucial for the manufacturing industry. It allows companies to streamline operations, reduce costs, and improve productivity. With digital tools, manufacturers can automate repetitive tasks and focus on more strategic work. This shift not only increases efficiency but also boosts job satisfaction among employees. Workers can spend less time on manual tasks and more time on problem-solving and innovation. Moreover, digitalization enables real-time data analysis, leading to better decision-making. Companies can quickly adapt to market changes and meet customer demands. Overall, embracing digitalization is key to staying competitive in today’s fast-paced business environment.
Key components of digital transformation in manufacturing
To fully embrace digital transformation, manufacturers need to understand its key components. At the heart of this transformation are Cloud-based ERP systems, which provide centralized control and easy access to business data from anywhere. Automation plays a significant role, streamlining production processes and reducing human error. Data analytics is another crucial component, allowing manufacturers to gain insights into operations, identify trends, and make informed decisions. Additionally, the use of advanced technologies like the Internet of Things (IoT) and artificial intelligence (AI) is on the rise, leading to smarter factories and more efficient workflows. Each of these elements contributes to a manufacturing environment that’s flexible, responsive, and ready for the future.
Challenges in manufacturing digital transformation
Despite the clear benefits of digital transformation, manufacturers face significant challenges when adopting new technologies. One of the biggest obstacles is the digital skills gap, where employees find it difficult to adapt to new software and systems. This slows down software adoption and can lead to reduced productivity and lower morale. Resistance to change is another common problem, with employees often hesitant to embrace new ways of working. Traditional training and onboarding methods may not be sufficient to address these issues, especially in large manufacturing companies with multiple locations.
Manufacturers must address these software adoption challenges to get the most out of their technology investments. If employees don’t use new software effectively, it can result in poor productivity and underperformance, leading to a failure to meet business goals. Companies risk their software investments falling short of expectations, potentially wasting resources and delaying progress. This is why robust training and ongoing support are crucial. Ensuring that employees are confident and capable with new technologies is key to a successful digital transformation and to maximizing the return on investment (ROI) in software and other digital tools.
Best practices for digital transformation in manufacturing
Investing in employee training software is imperative for manufacturing firms aiming to succeed in their digital transformation journey. By leveraging digital tools, companies can standardize the training process, making it more efficient and scalable. This ensures that all employees receive consistent and high-quality training, regardless of their location or role within the organization. Moreover, digital training platforms enable remote training, allowing employees to access learning materials from anywhere, at any time. This flexibility is particularly beneficial for manufacturing companies with dispersed workforces or multiple facilities.
Personalized learning paths are another crucial aspect of effective employee training. By designing training programs that align with individual roles, responsibilities, and career goals, companies can enhance employee engagement and retention. Employees are more likely to stay motivated and committed to their professional development when they see how training directly relates to their job and future growth opportunities. Personalized learning paths also help address the diverse skill levels and learning preferences within the workforce, ensuring that training efforts are tailored to meet each employee’s needs.
Continuous, on-demand employee support is essential for maintaining productivity and ensuring smooth operations during the digital transformation process. Providing employees with access to a self-service knowledge base allows them to find answers to their questions and access training resources whenever they need assistance. This empowers employees to take control of their learning and development, fostering a culture of continuous improvement and innovation within the organization. Additionally, on-demand support helps reduce reliance on traditional, time-consuming support channels, such as in-person training sessions or phone support, saving both time and resources for the company.
In summary, investing in employee training software with digital tools offers numerous benefits for manufacturing firms undergoing digital transformation. Standardizing training processes, facilitating remote training, creating personalized learning paths, and providing continuous, on-demand employee support are all essential elements for ensuring a successful transition to new technologies and maximizing the return on investment in training efforts.
How OnScreen Guidance addresses digital transformation challenges
A digital adoption platform (DAP) like OnScreen Guidance can address the challenges of digital transformation in manufacturing by providing real-time, in-app guidance that simplifies the learning process. With OnScreen Guidance, companies can create and deliver training content directly within the software applications that employees use daily. This approach reduces the need for lengthy, traditional training sessions and allows employees to learn while they work. The result is a shorter learning curve and a higher rate of software adoption, leading to increased productivity and job satisfaction.
OnScreen Guidance’s unique advantage lies in its simplicity. The platform is designed for business users and process owners, not just instructional designers, allowing for quicker content creation and distribution. This means that the people who know the processes best can create in-app tutorials and guides without extensive technical knowledge. By democratizing the creation of training materials, OnScreen Guidance helps minimize bottlenecks and fosters a more agile learning environment.
Additionally, OnScreen Guidance’s focus on operational perspective ensures that the training content is practical and relevant to the users’ needs. The platform’s lightweight design means it integrates smoothly with existing software, reducing disruptions to workflows. Furthermore, OnScreen Guidance’s in-app guidance can be customized for different roles and responsibilities, supporting the personalized learning paths essential for effective training. This customization and ease of use make OnScreen Guidance an ideal solution for manufacturing firms seeking to overcome the challenges of digital transformation and ensure successful technology adoption.
Final thoughts
In conclusion, digital transformation is revolutionizing the manufacturing industry, offering significant opportunities for increased efficiency, productivity, and competitiveness. However, to fully realize these benefits, manufacturers must address the challenges of software adoption and employee training effectively. The good news is that solutions like OnScreen Guidance can empower employees to embrace new technologies and workflows with confidence ensuring a smooth and successful transition. Ready to transform your operations? Contact us to learn how OnScreen Guidance can help.
FAQs
What is digital transformation in manufacturing?
Digital transformation in manufacturing involves adopting new technologies like cloud-based ERP, MES, and PLM systems to improve efficiency, streamline operations, and enhance customer experiences.
What challenges do manufacturers face during digital transformation?
Manufacturers often face digital skills gaps, slow software adoption, resistance to change, and difficulties in training and onboarding employees. These challenges can hinder productivity and reduce the return on technology investments.
How can a digital adoption platform (DAP) like OnScreen Guidance help with digital transformation?
A DAP like OnScreen Guidance provides real-time, in-app guidance, enabling employees to learn while they work. This approach reduces traditional training times, improves software adoption rates, and enhances employee productivity and morale.
What are the benefits of using a DAP for training and onboarding?
Using a DAP like OnScreen Guidance streamlines the training process, allows for personalized learning paths, and offers continuous, on-demand support. This results in faster onboarding, reduced training costs, and a better return on technology investments.
Why should manufacturing companies invest in OnScreen Guidance for digital transformation?
OnScreen Guidance’s simplicity and flexibility make it ideal for manufacturing companies. It allows business users to create custom training content without technical expertise, promoting faster software adoption and smoother digital transformation. This leads to improved efficiency and productivity, making OnScreen Guidance a valuable investment.
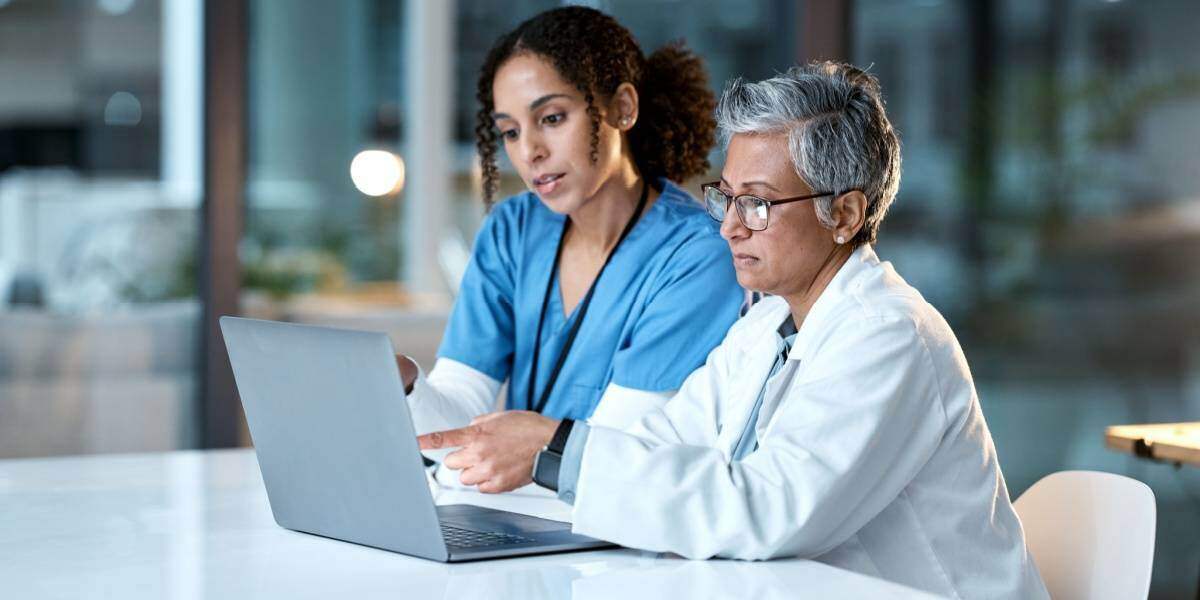
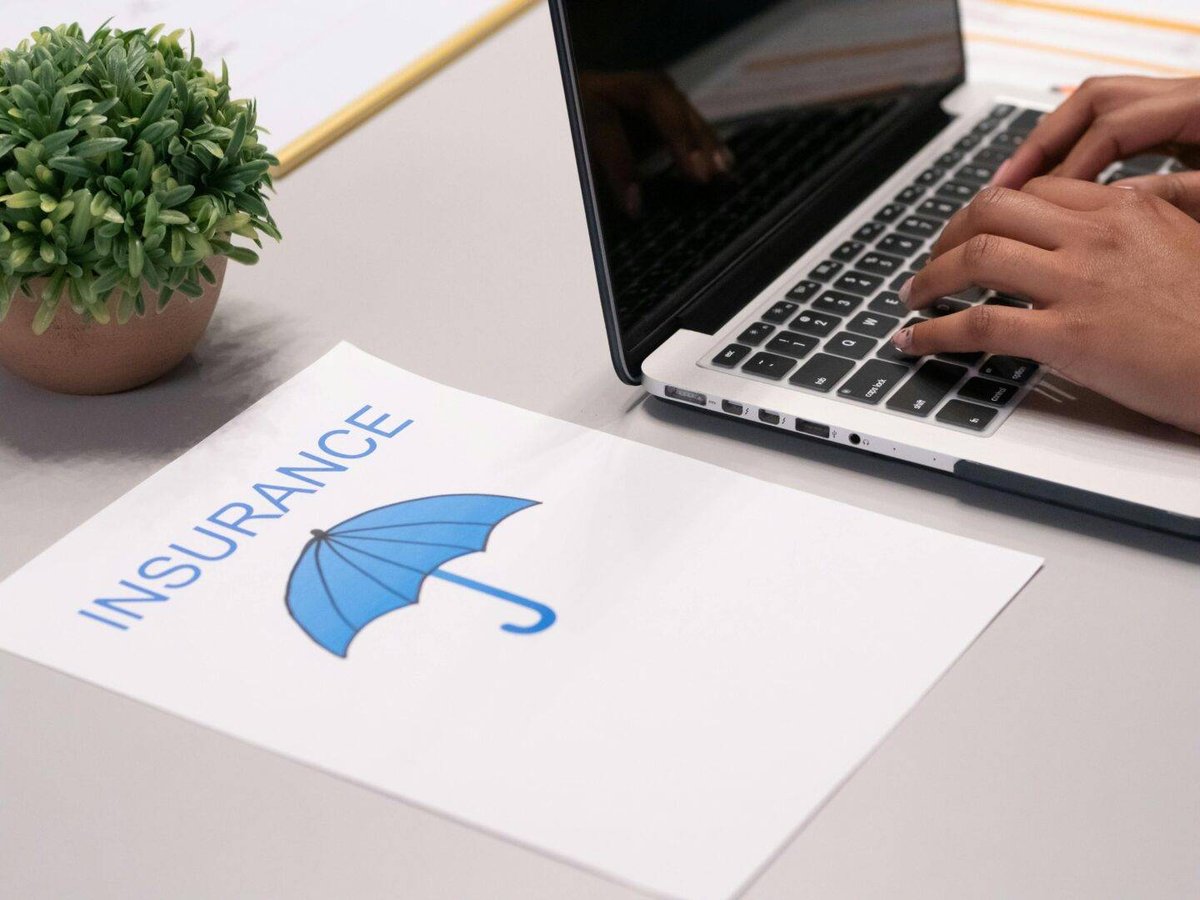
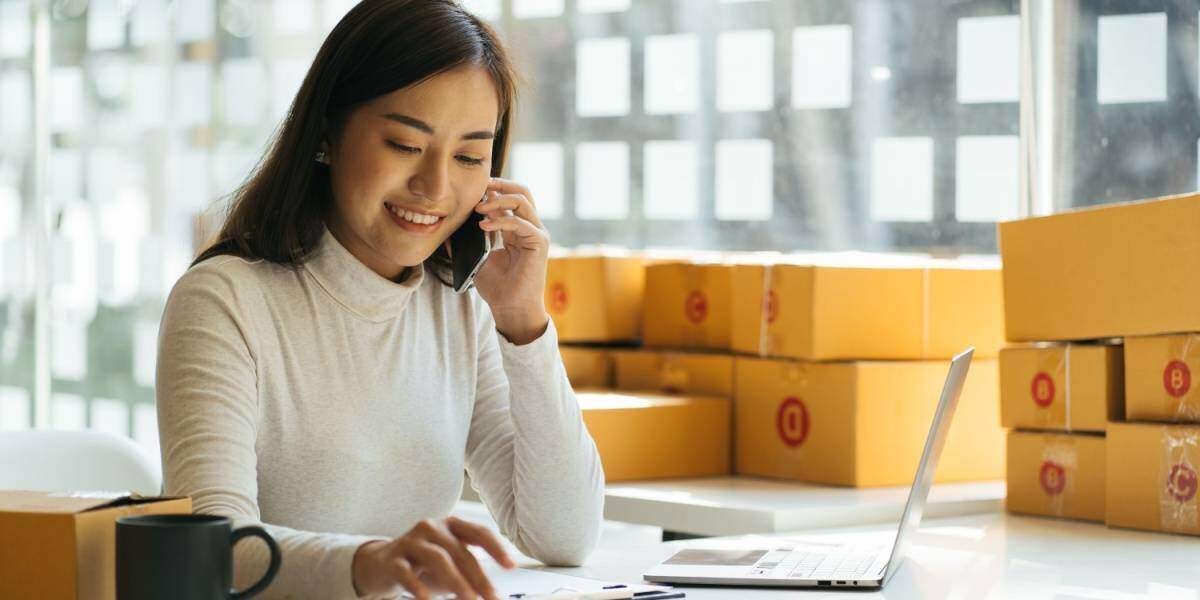