How L&D is helping the manufacturing industry address a skills shortage
Manufacturing is heavily exposed to the winds of technological change. Its ability to take advantage of new technology is dependent on highly skilled, high-performing employees. The challenge is how to develop, maintain, and retain that expertise.
New skills are needed to maintain growth
Manufacturing remains a powerful force in modern economies. In the UK the sector employs 2.5 million people and produces an annual output worth £183 billion. The manufacturing industry accounts for 50% of the UK’s total exports. Increasing automation and the use of AI are helping fuel the sector’s growth.
Yet, while much attention has been paid to the impact of the transformative power of new tech, there’s less awareness of the skills shortage that threatens that transformation and the industry’s competitiveness. Technology has removed plenty of low-skilled jobs from the sector, but at the same time, it’s created a greater demand for highly skilled people who are able to work with the new technologies. This new breed of worker is hard to find and challenging to keep. To retain knowledge workers businesses need to offer regular upskilling and career development opportunities.
Training must deliver performance
Effective training in the manufacturing industry is not only essential to work with the new technology, but it’s also critical in driving performance and ensuring compliance. New tools and products are continuously in development and coming on stream. The sector is highly regulated and the cost of failing to comply with regulations and standards can result in financial penalties, disruption to business, loss of productivity, and reputational damage.
The training landscape is complex
Training has to reach a diverse and sometimes large audience. Big businesses typically have multiple manufacturing sites. Whatever their size, manufacturing companies employ people in a variety of roles: production, sales, delivery, HR, IT, and so on. Their employees work in different locations: shop floor, warehouse, office, or on the road. Training needs also vary from the highly specialized, like computer software or operating machinery, to the broader-based courses in areas such as manual handling, environmental regulation, and health and safety. These requirements contribute to the relatively high cost of manufacturing training.
A positive onboarding experience is key to retention
Attrition rates in manufacturing can be high and add to staffing costs. Recent years have seen an exodus of highly experienced staff across the sector through retirement or to better opportunities elsewhere. Success in attracting and developing new hires depends on an effective onboarding process that sees them enter the workplace quickly with a clear idea of how and when they can swiftly progress and upskill.
Digital platforms offer an agile training solution
Manufacturing training is often disorganized with relevant learning content like SOPs created for individual workplaces and unevenly distributed. Digitizing all training and storing it in a learning platform helps centralize, standardize, and control content eliminating duplication and reducing risks of error and non-compliance.
Digital learning content can be accessed on a range of devices. This anytime, anywhere accessibility means training can be carried out in multiple locations removing the need to take employees away from their jobs and thus saving training costs. Mobile connectivity means training can be easily accessed by employees who travel or who work remotely.
Microlearning helps busy workers stay on course
Not everyone in manufacturing needs to complete all manufacturing training. Developing short chunks of digital content through microlearning helps personalize training making it more relevant to individual employees and the requirements of specific roles. Microlearning provides a way of delivering onboarding training that makes it more engaging but less obtrusive and helps support and accelerate new hire’s entry into work. Meanwhile, employees can take longer online courses at their own pace with integrated assessment features that test comprehension and compliance.
Simulating real-life challenges boosts learning
Simulation and scenario-based learning have particular relevance for the manufacturing industry. Highly realistic simulations can teach diagnostic and technical skills and provide a close-up understanding of how complex automated processes and tools work in a fail-safe environment. Scenarios test compliance by acting out relevant real-world situations. They present learners with a series of choices and give feedback on the consequences of those choices.
Retaining, updating and sharing knowledge keeps standards high
Manufacturing is heavily reliant on information sharing. Knowledge is crystalized and standardized in SOPs. Digitizing operating procedures helps maintain standards and makes SOPs quick and easy to update and disseminate across the business.
Learning platforms offer apps that facilitate collaboration so that the company’s knowledge base is up-to-date and expanding. The platforms also facilitate the sharing of knowledge through social learning features that allow employees to post tips and suggestions as well as create their own content. These knowledge-sharing options promote best practices and help ensure knowledge stays even when experienced employees depart.
Digital learning delivers upskilling at pace
Success in the manufacturing industry relies on highly skilled people who can perform to a consistently high level in a technologically complex environment. Online learning is a cost-effective and flexible way of equipping these people with the skills they need. Learning platforms offer the tools to standardize training, offer personal development, and make onboarding work. Easily accessible, adaptable training helps maximize employee performance, ensure compliance, and boost competitiveness in the manufacturing sector.
Find out how we’re helping the manufacturing industry address its skills shortage here.
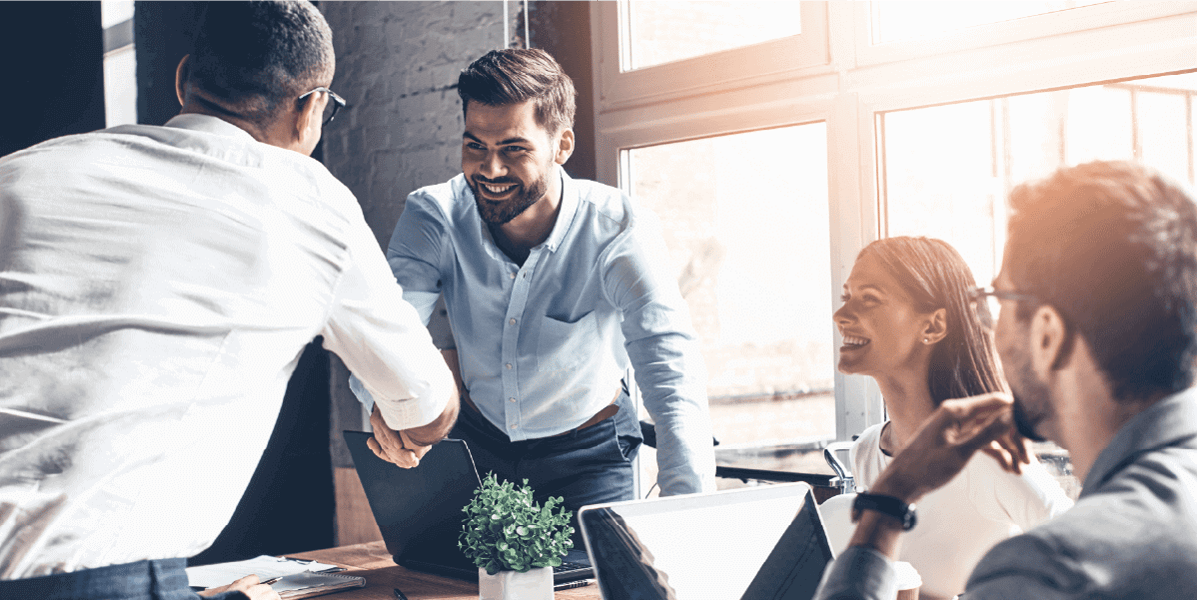
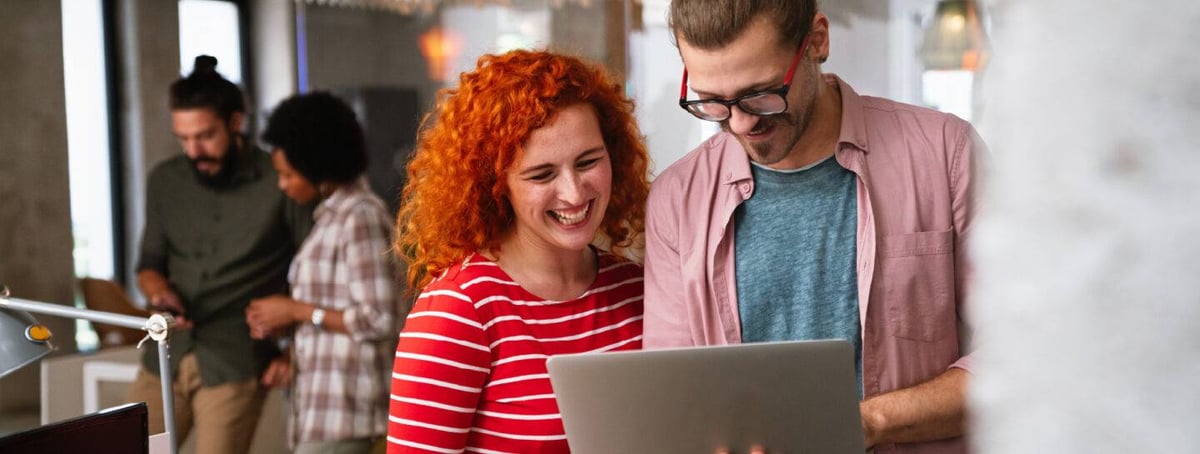
